Your key
issues
- High quality
- Optimised maintenance costs
- Respect for deadlines
- Safety of people and property at loading and unloading sites
- Guarantee of optimised operational management
Methodology
- Step 1
Step 1
- Step 2
Step 2
- Step 3
Step 3
- Step 4
Step 4
- Step 1
Step 1
- Step 2
Step 2
- Step 3
Step 3
- Step 4
Step 4
- Step 1
Step 1
- Step 2
Step 2
- Step 3
Step 3
- Step 4
Step 4
Step 1
Reconstruction of the history - Establishment of the Global Fatigue Index
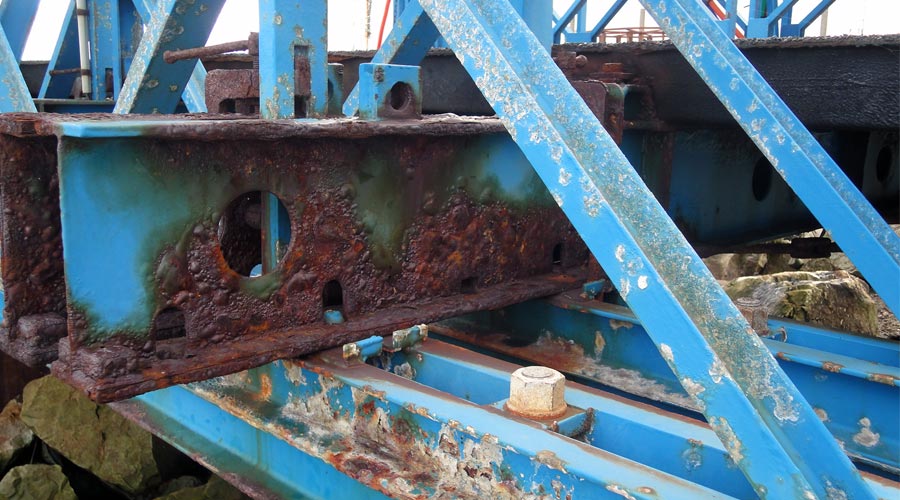
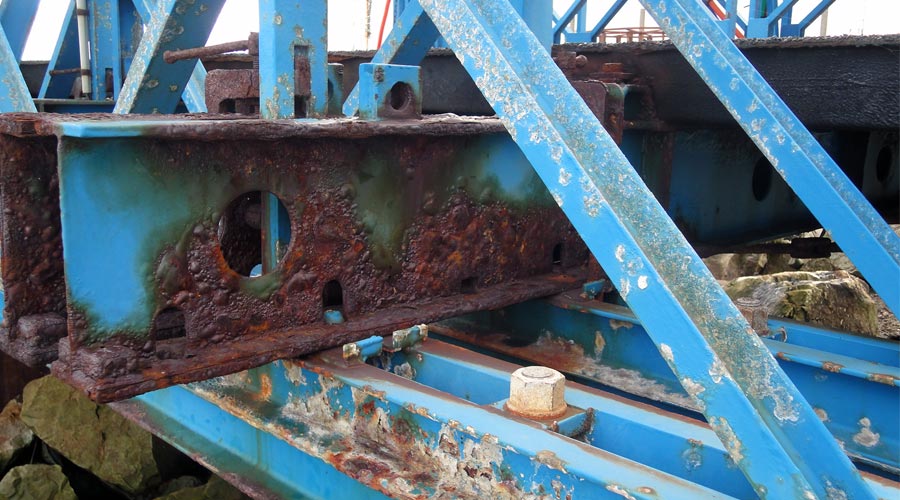
Objectives:
- To determine with the greatest possible precision the work cycles to which the equipment has been subjected
- To establish the overall fatigue index, i.e. that of the machine as a whole
More precisely:
- Original equipment classifications
- Recovering the technical elements of the history (of maintenance and operation)
- Exchanges with the personnel
- Technical visit of the equipment
- Comparison with the activity carried out
- Calculation of fatigue parameters (fatigue index, residual life) of the equipment as a whole and of the kinematic chains
- Definition of load cases
Step 2
Modelling and stress calculations
Identification of critical assemblies and components
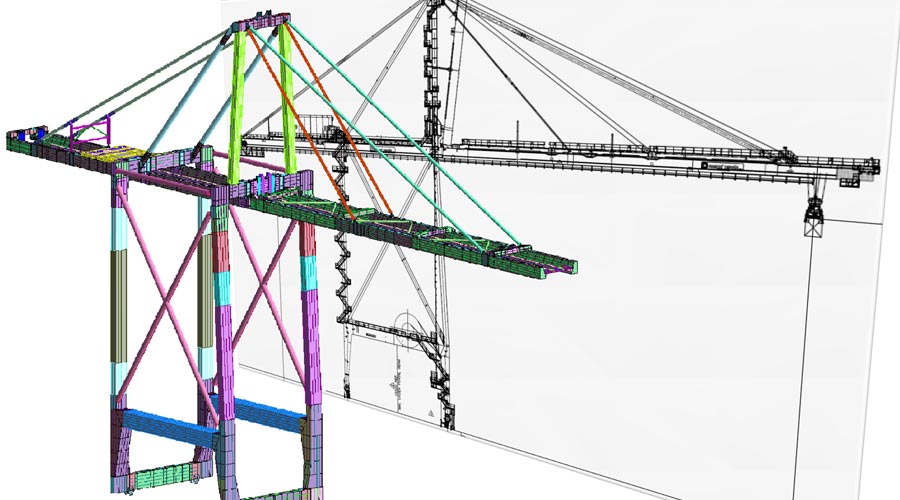
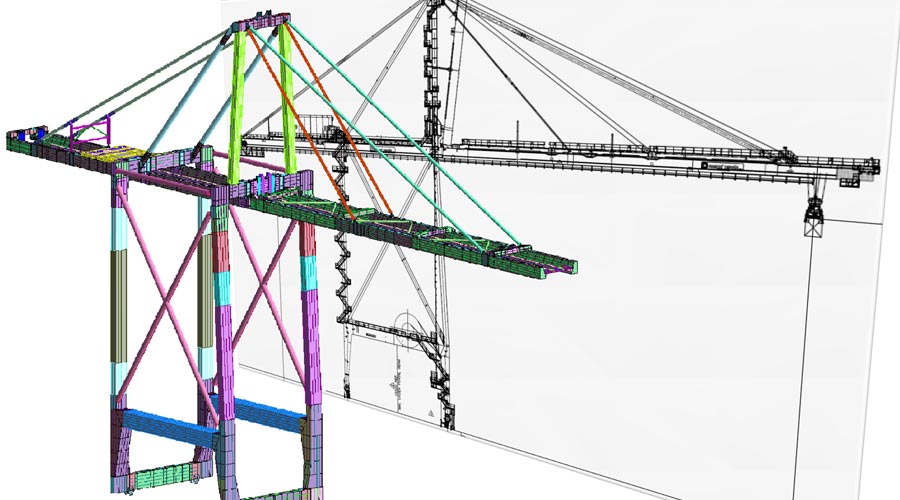
Objectives:
- To determine, through modern and accurate modelling, the stresses experienced by the different assemblies of the aircraft, for the different load cases
- To identify the "critical" parts of the equipment, based on 3 parameters: strength stresses, fatigue stresses and our experience with similar assemblies that have caused problems in the past
More specifically:
- Adapted modelling from drawings and/or site surveys
- Application of the various load cases according to the reference system and determination of the stresses
- Reconstitution of stress spectra and number of fatigue cycles undergone by the assemblies
- Notching of the connection (and verification on site)
- Ageing factor and number of remaining cycles (fatigue and lifting cycles)
- Determination of critical connections by maximum stress value, ageing factor or experience
- Development of a checklist for the next stage of the assessment
Step 3
Inspection of critical areas
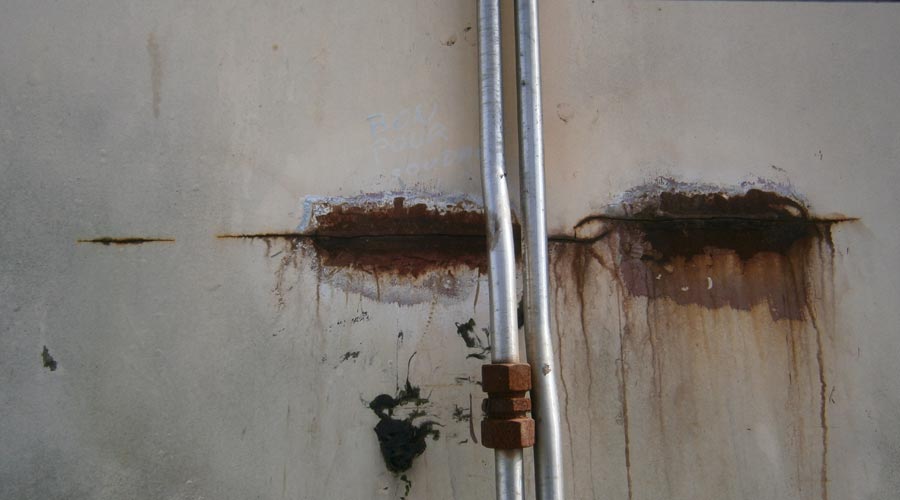
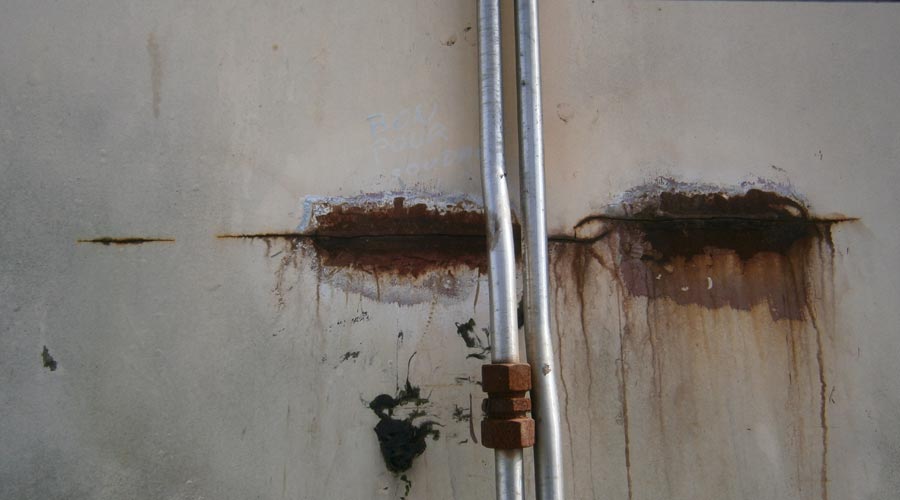
Objective:
- To carry out suitable inspections (visual checks, NDT) of the various areas identified as critical in the previous step, in order to verify their integrity
More specifically:
- Visual inspections of assemblies and components
- Non-destructive testing (NDT)
- Thermography
- Vibration analysis
- Oil analysis
Step 4
Summary and control plan
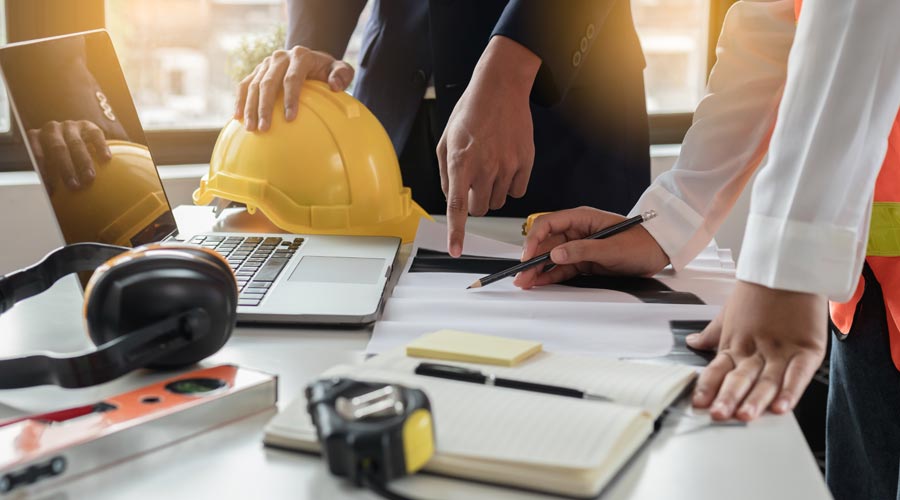
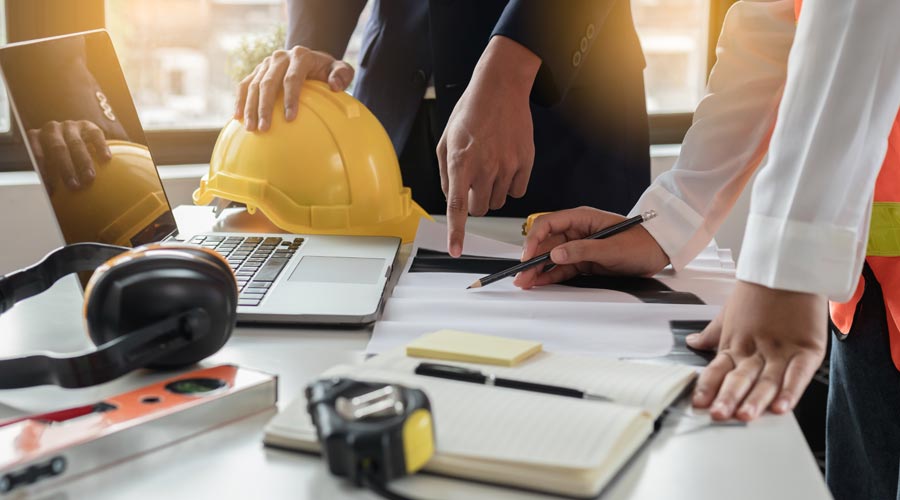
Objective:
- To synthesise all of the above and make recommendations
- Draw up an optimised control plan, which precisely defines the areas to be controlled and the associated technical means and frequency, in order to effectively control the risk of structural disorders.
More specifically:
- Proposal of inspection plans
- Definition of the type of inspection (visual, magnetic particle, ultrasonic, dye penetrant, ACFM, etc.)
- Definition of frequencies
- Drawing up of inspection sheets
- Determination of the "safe operation" period
- Recommendations to ensure continuity and safety of operation
Why choose
Aquass?
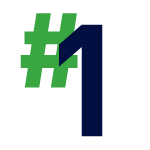
Full support
Experts in heavy lifting equipment, port, industrial, or other, Aquass masters the design, technology, risks and regulations.
Assistance for all phases of the equipment life cycle, from the analysis of the need to its dismantling.
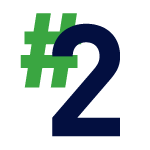
The reference in terms of fatigue diagnosis
Aquass has been performing fatigue diagnostics on lifting equipment since the risk was first identified.
Our methodolgy for analysing and calculating residual service lift is unrivalled, enabling the durability of a machine to be controlled by optimised overhaul.
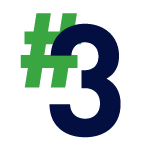
A relevant and pragmatic opinion
Aquass knows the problems of operators (availability, deadlines, costs, ...).
Our recommendations are technically relevant and pragmatic with regard to your constraints.