The challenges
of modelling
- Obtain the maximum stresses and extreme stresses in all structural assemblies of a machine during its operation
- To allow calculation of the residual life of assemblies as a function of the stresses they are subjected to
- Identify areas that could present a risk of structural disorder
- To allow the implementation of a targeted surveillance on these critical areas
Calculations
From calculations for reliability studies: FMECA, fault trees, Markov graphs (quantitative and qualitative), to sizing studies of structures and mechanisms and fatigue calculations (FEM, EN, BS, etc.), according to calculation rules (bar, surface and 3D), our experts carry out all of the calculations required to establish the most suitable models for your needs.
Modelling
Modelling
methodology
The structural design rules defined in the FEM are based on classical beam theory, so bar-type finite element modelling is particularly suitable but the lessons learned are very limited.
As the technological means have greatly evolved since the definition of the FEM rules, we now use the surface finite element methodology.
This methodology has a number of advantages:
- Bar-type finite elements provide nominal stresses at the neutral fibre of the modelled elements, while surface-type modelling allows stress concentrations in the connection areas to be highlighted.
- The drafters of the FEM rules, aware of the existence of stress concentrations not taken into account in calculations, even those based on bar modelling, defined the maximum permissible stress values by dividing the value of the elastic limit of the material by a coefficient of between 1.50 and 1.10, depending on the load case. Surface modelling allows stress concentrations to be analysed in a much less arbitrary manner on a case-by-case basis and to compare the maximum values with the yield strength of the steel used.
- The results for variable inertia elements or box structures more generally are much more relevant in surface modelling because the neutral fibre eccentricities of the modelled elements are taken into account much more accurately.
With these arguments in mind, and with the design of lifting equipment having evolved greatly over the years (less lattice structure and much more box structure in particular), it is not very reasonable at present to be satisfied with a simple bar-based model.
Tools


The software used is Robot Structural Analysis. The load cases of our models are applied in accordance with the design rules (FEM, NFEN13001).
Robot Structural Analysis allows us to obtain the most unfavourable stresses for the structure, for several working positions of the equipment, as well as the extreme stresses encountered during operation, in order to be able to calculate the life of the structure's assemblies.
We are also working on Ansys or Caesar type software, which gives the ability to see how designs will perform in several real world scenarios, while reducing the need for costly physical testing.
Examples of
modelling
Why choose
Aquass?
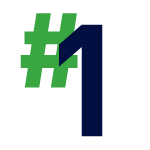
Full support
Experts in heavy lifting equipment, port, industrial, or other, Aquass masters the design, technology, risks and regulations.
Assistance for all phases of the equipment life cycle, from the analysis of the need to its dismantling.
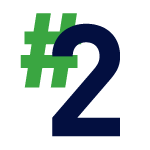
The reference in terms of fatigue diagnosis
Aquass has been performing fatigue diagnostics on lifting equipment since the risk was first identified.
Our methodolgy for analysing and calculating residual service lift is unrivalled, enabling the durability of a machine to be controlled by optimised overhaul.
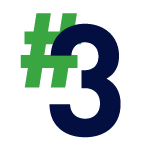
A relevant and pragmatic opinion
Aquass knows the problems of operators (availability, deadlines, costs, ...).
Our recommendations are technically relevant and pragmatic with regard to your constraints.