Key issues for
safe construction
To anticipate technical, human and environmental risks and remain in compliance, Aquass secures the monitoring of your lifting equipment around 3 major axes:
- Controlling technical risks by detecting incidents and resolving them as quickly as possible
- Safety of people and property
- Offer a better understanding of the behaviour and use of your equipment
Digilife
Digilife +
Discover Digilife solutions
Digilife
Continuous monitoring
The parameters with a single or major influence in the different risks concerning lifting equipment are the following:
Breakdown due to lack of resistance | ![]() |
Abnormal peak load |
Collapse by buckling | ![]() |
Abnormal peak load |
Deformation or even collapse through warping | ![]() |
Abnormal peak load |
Fatigue cracking and failure | ![]() |
Spectrum factors, number of cycles and maximum abnormal loads |
An overview of fatigue
Digilife allows :
- Acquire relevant information from the device's own sensors
- Process the information by calculating the parameters representative of the cumulative fatigue damage
- To ensure the storage of the parameters
- Keeping the last value in memory or delivering it remotely at a fixed frequency or on demand:
- The level of ageing of structures and kinematic chains
- The values of the parameters for calculating the fatigue rates
Recording of incidents
In the event of an incident Digilife will store the essential parameters for 5 seconds (before and after the incident) and retransmit them for recording.
List of some incidents that may trigger a recording:
- Maximum cable voltage T1, T2 or (T1+T2) exceeded
- Too large a difference between voltages (T1-T2)
- Lifting fault
- Steering fault
- Anti-snag fault
- Distribution fault
Digilife +
Close supervision of structures
The main function of Digilife in terms of fatigue compares in real time the ageing of the machine as a whole and of its kinematic chains with the overall conventional ageing predicted by the manufacturer at the time of its design.
The ageing of the machine as a whole is essential, but to be even more relevant, attention must be paid to the ageing of each welded assembly making up the structure. This makes it possible to better target and anticipate controls.
DigilifePlus now allows the residual life of welded assemblies identified as critical to be processed, by the difference between their actual calculated maximum life and the life consumed according to the usual real time supervision.
New: 3D modelling of your equipment
Modelling, which is one of the specialities of Aquass, enables the extreme stresses and stress spectrum factor of each assembly to be defined for each cycle as a function of loading. Aquass can therefore calculate the fatigue damage generated by each cycle, for each assembly.
DigilifePlus incorporates the values of the residual life and fatigue rate calculation parameters for each monitored assembly from the post-processing of the modelling results.
Optimisation of the test plan
The knowledge of these residual lifetimes in real time and on demand allows DigilifePlus to optimise the structural inspection plan established by Aquass, and to improve its relevance to safety in particular, by taking into account the actual fatigue rate of each assembly identified as critical.
DigilifePlus thus becomes a structured structural maintenance management tool without equivalent, by establishing a reasonable and optimised control plan based on the analysis of the real risks attached to fatigue damage.
As insurers are increasingly sensitive to the conditions of organisation and rigour of maintenance operations, especially after damage, this type of approach is likely to reassure them.
About
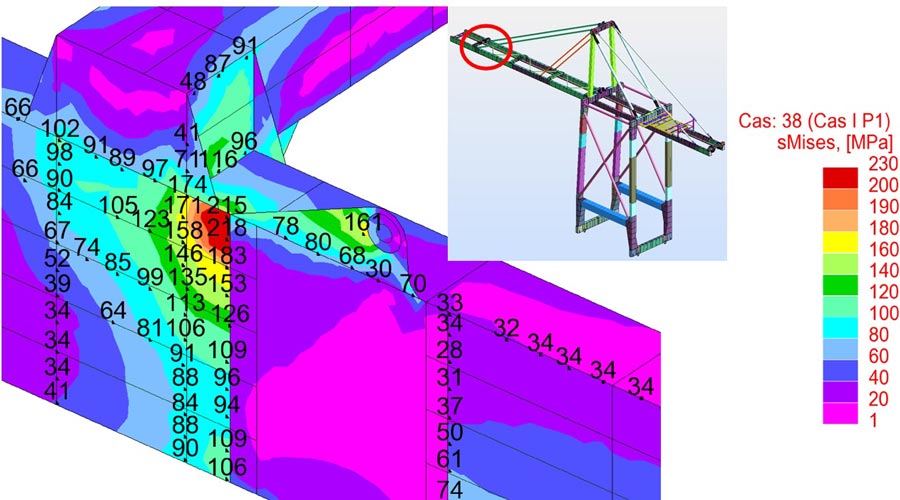
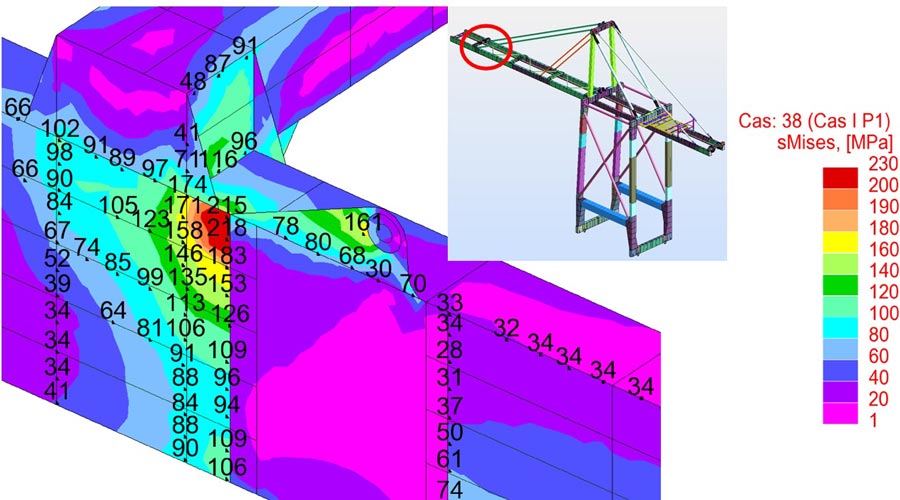
Digilife was developed in collaboration with our partner AES (Automatisme Etudes Services).
These customers who trust the Digilife solution:
- ABB Sweden
- SIEMENS
- CARGOTEC
- ZPMC
- DCNS Brest
- Joseph Paris SA
- REEL
- PSDF - Port Sud de France
- PACECO
Why choose
Aquass?
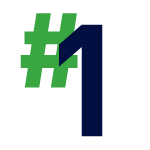
Full support
Experts in heavy lifting equipment, port, industrial, or other, Aquass masters the design, technology, risks and regulations.
Assistance for all phases of the equipment life cycle, from the analysis of the need to its dismantling.
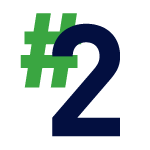
The reference in terms of fatigue diagnosis
Aquass has been performing fatigue diagnostics on lifting equipment since the risk was first identified.
Our methodolgy for analysing and calculating residual service lift is unrivalled, enabling the durability of a machine to be controlled by optimised overhaul.
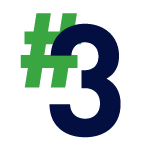
A relevant and pragmatic opinion
Aquass knows the problems of operators (availability, deadlines, costs, ...).
Our recommendations are technically relevant and pragmatic with regard to your constraints.